Benefits of Lean Management
- Manage Team/Process Complexity
- More Efficient Business Processes
- Better Management of Changing Priorities
- Better Project Visibility at the Team Level
- Increased Team Productivity
- Reduced Lead Time
- Increased Team Morale
- Improved Visibility to Stakeholders
- Reduced Costs
- Predictable Delivery of Customer Value
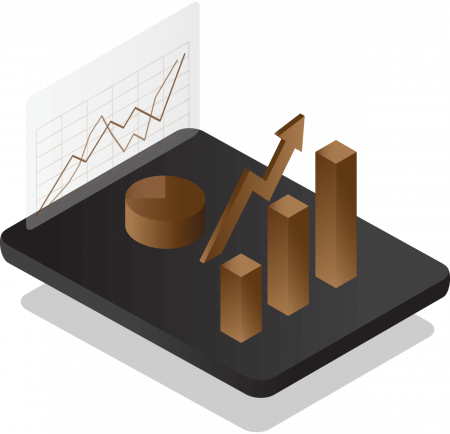